Inventory Management: Definition, Key Methods, How It Works, and Examples
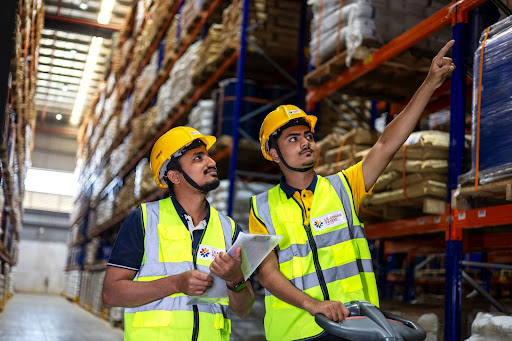
In today’s fast-paced business environment, effective inventory management is crucial for companies aiming to meet customer demands while optimising costs. This comprehensive guide delves into the definition of inventory management, its operational processes, key types of inventory management methods, accounting considerations, and real-world examples to provide a holistic understanding of this vital business function.
What Is Inventory Management?
Inventory management is the systematic process of ordering, storing, using, and selling a company’s inventory. This includes managing raw materials, components, and finished products, as well as overseeing warehousing and processing of such items. The primary goal of inventory management is to ensure that a business always has the right products in the right quantities to meet customer demand without incurring excess costs or stockouts.
Effective inventory management encompasses several key activities:
- Ordering: Determining what products are needed and in what quantities, and placing orders with suppliers accordingly.
- Storing: Safely and efficiently housing products until they are needed for production or sale.
- Using: Allocating inventory for production processes or fulfilling customer orders.
- Selling: Ensuring products are available and in good condition for customers to purchase.
There are different types of inventory that businesses manage:
- Raw Materials: Basic inputs used in the production process.
- Components: Semi-finished goods that will be used to create the final product.
- Finished Products: Completed goods ready for sale to customers.
Various inventory management methods help businesses maintain optimal inventory levels. These methods include Just-in-Time (JIT), Materials Requirement Planning (MRP), Economic Order Quantity (EOQ), and Days Sales of Inventory (DSI), each offering unique strategies to balance supply and demand effectively.
How Inventory Management Works?
Inventory management operates through a structured process that can be broken down into three key steps:
- Purchasing Inventory: This involves sourcing and acquiring the necessary raw materials, components, or finished goods from suppliers. Effective purchasing requires understanding market demand, negotiating favourable terms, and ensuring timely delivery.
- Storing Inventory: Once acquired, inventory must be stored safely and efficiently. This includes organising products in warehouses or storage facilities, implementing tracking systems, and ensuring proper environmental conditions to maintain product quality.
- Profiting from Inventory: The final step is utilising the inventory to generate revenue. This could involve selling finished products to customers or using raw materials in the production process to create sellable goods.
By meticulously managing each of these steps, businesses can optimise their inventory levels, reduce costs, and enhance profitability.
The Benefits of Inventory Management
Inventory is one of the most valuable assets for businesses, especially in sectors like retail, manufacturing, and food services. There are numerous benefits of inventory management if done effectively:
- Meeting Customer Demand: By maintaining appropriate inventory levels, businesses can promptly fulfil customer orders, enhancing satisfaction and loyalty.
- Cost Reduction: Proper inventory management helps in minimising holding costs, reducing waste from spoilage or obsolescence, and avoiding overstocking.
- Improved Profitability: Efficient inventory practices ensure that capital is not unnecessarily tied up in stock, allowing for better cash flow and investment opportunities.
Conversely, poor inventory management can pull you away from the benefits of inventory management and lead to significant risks, including:
- Overstocking: Excess inventory can result in increased holding costs and potential waste, especially for perishable goods.
- Stockouts: Insufficient inventory levels can lead to missed sales opportunities and dissatisfied customers.
- Theft and Loss: Without proper tracking, inventory is susceptible to theft or loss, impacting profitability.
To mitigate these risks, businesses employ various inventory management methods, ranging from manual tracking using spreadsheets to sophisticated Enterprise Resource Planning (ERP) systems and AI-driven solutions. Industry-specific examples include:
- Retail & Fashion: Managing seasonal demand fluctuations by adjusting inventory levels accordingly.
- Food Industry: Implementing strict rotation policies to avoid waste and spoilage of perishable items.
- Manufacturing: Ensuring continuous availability of raw materials to prevent production delays.
Key inventory management strategies such as Just-in-Time (JIT) and Materials Requirement Planning (MRP) assist businesses in aligning their inventory levels closely with actual demand, thereby optimising resources and reducing waste.
Understanding Inventory in Accounting
In financial accounting, inventory is classified as a current asset, representing goods available for sale or raw materials used in production. Accurate measurement of inventory is essential before recording it in financial statements, as it directly affects the cost of goods sold (COGS) and overall profitability.
Inventory management systems play a pivotal role in tracking stock levels, ensuring that records reflect actual quantities on hand. This accuracy is crucial for financial reporting and operational decision-making.
There are several inventory accounting methods, including:
- First-In, First-Out (FIFO): Assumes that the oldest inventory items are sold first, which can be beneficial in times of rising prices as it matches older, lower costs with current revenues.
- Last-In, First-Out (LIFO): Assumes that the most recently acquired items are sold first, which can be advantageous for tax purposes in certain scenarios but is not permitted under International Financial Reporting Standards (IFRS).
- Weighted-Average Costing: Calculates an average cost for all inventory items, smoothing out price fluctuations over time.
Inventory is typically categorised into four main types:
- Raw Materials: Unprocessed materials used in production.
- Work in Process (WIP): Items that are in the production process but not yet complete.
- Finished Goods: Products that are completed and ready for sale.
- Merchandise Inventory: Goods purchased for resale without any further processing.
Understanding these categories and accounting methods enables businesses to value their inventory accurately, ensuring financial statements reflect true economic conditions.
Inventory Management Methods
Effective inventory management is vital for seamless business operations. Various methods have been developed to address different operational needs. Here are some of the most common inventory management methods:
1. Just-in-Time Management (JIT)
Just-in-Time (JIT) is an inventory strategy that originated in Japan, primarily associated with Toyota’s manufacturing processes. JIT aims to increase efficiency and reduce waste by receiving goods only as they are needed in the production process, thereby minimising inventory costs.
While JIT helps businesses save money by reducing the amount of inventory held, it also comes with risks. For instance, supply chain disruptions or sudden spikes in demand can lead to stockouts, as there is little to no buffer stock available.
2. Materials Requirement Planning (MRP)
Materials Requirement Planning (MRP) is a system that relies on sales forecasts to ensure that raw materials are available for production when needed. By analysing production schedules and inventory levels, MRP helps businesses plan their purchasing and manufacturing activities effectively.
For example, a manufacturing company might use MRP to determine the exact quantity of components required to meet anticipated customer orders. However, inaccurate forecasting can lead to shortages or excess inventory, highlighting the importance of precise data input.
3. Economic Order Quantity (EOQ)
Economic Order Quantity (EOQ) is a formula used to determine the optimal order quantity that minimises the total costs of ordering and holding inventory. The EOQ model balances the trade-off between the costs associated with ordering inventory and the costs of holding it.
Businesses use EOQ to identify the most cost-effective quantity to order, reducing the frequency of orders while maintaining sufficient stock levels. For instance, a retail store might use EOQ to determine how many units of a product to order at a time to minimise both purchasing costs and storage expenses.
4. Days Sales of Inventory (DSI)
Days Sales of Inventory (DSI) is a key performance metric that indicates how long a company takes to sell its inventory. It is calculated using the formula:
DSI = (Average Inventory / Cost of Goods Sold) x 365
A lower DSI means a company is selling its inventory quickly, reducing storage costs and improving cash flow. However, an extremely low DSI could indicate that a business is struggling to maintain adequate stock, leading to frequent stockouts. On the other hand, a high DSI might suggest excess inventory, which could increase holding costs or lead to obsolete stock.
Inventory Management Red Flags
Effective inventory management is essential for maintaining a company’s financial health and operational efficiency. However, poor inventory management methods can lead to critical issues that impact profitability. Identifying red flags early can help businesses avoid financial losses, inefficiencies, and disruptions in the supply chain.
Common Inventory Management Red Flags:
- Frequent Stockouts: Running out of inventory often indicates poor demand forecasting or supply chain issues.
- Excessive Overstocking: Holding too much inventory ties up capital and increases storage costs.
- Inconsistent Inventory Records: Discrepancies between actual stock and recorded data can lead to operational delays.
- High Holding Costs: Rising warehousing costs due to overstocking can affect the company’s bottom line.
- Slow Inventory Turnover: Products that remain unsold for extended periods can lead to losses due to obsolescence.
By addressing these red flags, businesses can ensure smoother operations and reap the benefits of inventory management.
What Are the Four Main Types of Inventory Management?
There are four primary types of inventory management that businesses use to streamline operations:
- Perpetual Inventory Management – This method continuously updates stock levels using real-time tracking.
- Periodic Inventory Management – Inventory is counted at specific intervals rather than continuously.
- Just-in-Time (JIT) Inventory Management – Stock is replenished only when needed, reducing storage costs.
- Material Requirements Planning (MRP) – Inventory levels are managed based on production schedules and demand forecasts.
Each of these types of inventory management offers unique advantages, and businesses must choose the one that aligns with their operational goals.
How Does Apple Use Inventory Management
Apple, one of the world’s most successful companies, has mastered inventory management to maintain efficiency and profitability. The company follows a Just-in-Time (JIT) inventory management approach, minimising excess stock while ensuring a seamless supply chain.
Tim Cook, Apple’s CEO, is known for his expertise in inventory management methods. Under his leadership, Apple has streamlined its production and supply chain, reducing unnecessary inventory and improving cost efficiency. The company uses advanced forecasting tools, automation, and data analytics to optimise its inventory, ensuring that demand is met without excessive stock.
Apple’s approach is an excellent example of how best inventory management practices can enhance profitability and efficiency.
Inventory Management Example
Consider a retail company that sells seasonal clothing. The business must manage inventory carefully to meet demand without overstocking.
Scenario:
- The company uses inventory management methods like Economic Order Quantity (EOQ) to determine how much stock to order at a time.
- It leverages Just-in-Time (JIT) inventory management to avoid excessive stockpiling.
- The company monitors Days Sales of Inventory (DSI) to track how quickly it sells inventory.
By adopting best inventory management practices, the retailer ensures that it meets customer demand while avoiding unnecessary costs.
Conclusion
Understanding what is inventory management and implementing the right inventory management methods is crucial for business success. Whether a company operates in retail, manufacturing, or e-commerce, effective inventory management helps optimise stock levels, reduce costs, and improve efficiency.
By identifying red flags, choosing the right types of inventory management, and following best inventory management practices, businesses can gain a competitive edge and enhance profitability.
Frequently Asked Questions
1. What’s the difference between inventory management and inventory optimisation?
A: Inventory management focuses on tracking, storing, and controlling stock, while inventory optimisation ensures that businesses have the right stock levels to meet demand efficiently.
2. What’s the difference between inventory management and inventory control?
A: Inventory management covers the entire process, from purchasing to selling inventory, while inventory control ensures stock accuracy and prevents losses due to theft or spoilage.
3. What’s the difference between an SKU and a UPC?
A: An SKU (Stock Keeping Unit) is a unique identifier for products within a company, while a UPC (Universal Product Code) is a barcode used for product identification across different retailers.
4. What’s the difference between inventory and stock?
A: Inventory includes raw materials, components, and finished goods, while stock typically refers to finished products ready for sale.